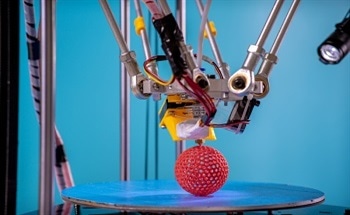
Manufacturing additive, ALSO Called Three-Dimensal (3D) Printing, HAS BECOME A ROBUST Production Technology With Many Advantages Over Convention Technical Manufacturing, Including Lower Energy and Material Requirements.
Three-dimensional printing technology is based on the targeted, layer-by-layer deposition of a source material that is cured or otherwisted solidified with health to produce a final three-dimensional product. Lasers are a very effective Heat Source for this Technology Becuse a Laser beam can Provide a Large Ament of Highly Focused Energy, Allowing for a High Degree of Precision and Speed for a Wide Variety of Materials.
Stereolithography (SLA), Selective Sintering Laser (SLS) and Selective Laser Melting (SLM) 3D Printers All Use Lasers to Produce 3D Objects, Although all Three Use Lasers in Different Ways. In fact, these uses May uses different Kinds of lasers.
YTTERBIUM-FIBER LASERS ARE COMMONLY USED by Major Players in Additive Manufacturing. Carbon dioxide lasers are typically used on polymer power, while frequency tripled nd: yvo4 lasers are often used to cure photopolymer resins.
New Laser Technology is Always Being Investigated and Adapted for 3D Printing Purposses. Helium-Cadmium Lasers and Argon Excimer Lasers Are Being Examined for Sla Making, While Femtosecond Lasers Are Looking Increasingly Promising for Printing the Materials with High melting temperatures or thermal diffusify.
Stereolithography
Stereolithography Ultraviolet Laser to Precisely Cure A Photosensitive Resin to Create A Product Based on 3D Digital Model. The Standard SLA 3D Printer Device Includes A Laser, A Tank for Resin and A Build Platform, Which Sits on An Elevator.
The SLA FABORTION PROCESS STARTS With the Resin Tank Being Girl. Once the tank is full, the build platform is dropped into the resin tank, to the point it is a single layer in height aboo the floor of the tank. The laser is then situated below the tank and direct up through the transparent tank floor. Laser light then traces through the tank in the outline of the First Layer of the 3D Design, Curing the resin as it draws. The Build Platform then Moves Up After Each Successive Layer of the Object is Drawn UNTIL the ENTIRE SEQUENCE IS FINISEHED AND THE OBJECT IS FULLY FORMED.
Selective Sinteering Sinteering
Selective Laser Sintering also Makes Use of A Laser; However, The System is who different from an SLA Device. The Main Difference Between the Two is Source Material. Rather Than a Photosensitive Resin, Sls Produces Items from a Fine-Powder Polymer, Which The Laser Fuses Together to Create Products.
Similar to an Sla Printer, an Sls Printer is included of a laser, Powder Bin and A Build Platform Connected to an Elevator.
The SLS MADIFICATION PROCESS STARTS With the POWDER BIN Being Daughter with POWDER TO A Height Equivalent to A Single Layer of the Object Being Printed. Laser Light then Traces The First Layer, Sinteering the Powder Into a Cohesive Unit. Successive Layers of Powder Are Added and the Platform then Moves Vertically in Layered Incrects to Fabricate Layer Layer, One On Top of Another, in Succession Until The Object Has Been Completed.
UNLIKE SLA, support structures are not necessary for sls, given that the surrounding, non-suntered power acts as a supportive material. This allows the Manufacturing of More Inclusive Objects and Shapes.
Selective laser melting
selective laser melting (SLM) is a different kind of additive manufacturing process use to make metal product in three dimensions. The process used a metallic power that is liquidated with a laser in targeted areas. Going Through Successive Powder Layers, The Sls System Heats Metallic Power Based on 3D Computer Model. Each Powder Layer is Added on Top of A Melted Layer the Object is Completed.
SLM Manufacturing is commonly used in aerospace. The Technology is Particularly Well-Suite to Making the intrigate parts Commonly Found in That Conents. SLM has also been used in medicine. Prosthetics made using slm can be customized to the particular anatomy of the individual patient.