Virtual Reality (VR) and increased reality (AR) Are Some of the Hottest Multidisciplinary Technology Trends Right Now, Integrating Computer, Various Sensor, Graphic Image, Communication, Measurement and Control Multimedia, Artificial Intelligence, and Other Technologies.
VR Commonly Employs Behavioral Interfaces and Computer Programs to Allow Users Interact with Each Other and to Simlate the Behavior of 3D Objects in A Virtual Environment. VR implies a complete immersion experience that shots out the physical world.
In contrast, ar adds digital elements to a live view often by using the camera on a smartphone. Example of increased reality experience include snapchat lenses, the game pokemon go and navigation system that superprimpose a route over the live view of the road.
While Ar can work on Existing Display Screens Such As Smartphones and Other Monitors, Most People Associate Vr with More Less Bulky Headset Displays.what that means is that mimicking human sensory system system at the moment is often limit to audio and video channels, and requires box and rigid devices.
Interactive Textile Electronic Devices Will Provide Follow -up Platforms for VR/AP Applications of their Excellent Performance and Unique Immersive Features Such As Lightweight, Handiness, Flexibility, Comfort, and Low Strain Even Under High DEFFORMATIONS.
Textile-Based Systems Offer A Better Experience in Emerging VR/AP Applications With Respect to Other Sensory Interactions Than Just Audial and Visual Interactions. Furthermore, textile Devices Enable The Wearable VR/AR System to Be Smaller, Softer, and More Comfortable, Which Broadens the Range of VR/AP Applications.
DRUDCTIVE INTRIINS NANOMATERIALS SUCH AS CARBON NANOTUBES AND METALLIC NANOWRIES AS WELL AS NANOSCALE Devices such as triboelectric nanogenerators are key to develop these electronic textiles.
A Review article in Advanced Functional Materials ("Textile Electronics for VR/AP Applications"), Compiled by Researchers from the Hong Kong Polytechnic University, Address the State-of-The-Art Textile-Based VR/AR Devices, Systems, and Applications.
The Authors First Introduce The Field of Textile Electronics (E-Textiles) Including Their Definition, Classification, Manufacturing Technology, and System Architecture.to Catch Up On the Latest Developments in E-Textiles and Wearable Electronics) Take A Look at our collection of nanowerk spotlight on the subject.
Apart from Actuators and Electrodes, an important part of e-textiles are sensors to detect physical and scalp stimuli to acquire abuant information about the environment as a basis of interaction. Considering the Characteristics of Textiles, A Sensor in Textile Format can be flexible, sustainable, biocompatible, and lightweight. The Sensors can be used in VR/AR Systems as Strain, Pressure, Temperature, Gas, Smell, and Multifunctional Sensors.
For instance, strain sensors can transduce mechanical motion into an electrical signal to monitor large-scale and small-screen motions; These find applications in Healthcare, Sports, and Robotic Industries.
Sensory stimuli Provide people with a coherent perception of the world. Textile Electronic Devices Are An Excellent Platform for People to Simultaneously Experience Audio, Video, Allowing Haptic, Multimodal Sensory Inputs, and Movement in Graphically Rendered Objects OR Environment. Perception Devices Transform Various Perception Models in the Virtual World to Multi-Channel Stimuli (EG, Tactile, Visual, and Hearing Signals) for Detection.Following Their Discussion of E-Textiles, The Authors then Introduce Interactive Textile Devices Used in VR/AR Systems. This is followed by a presentation of Various Manufacturing Processs and examines certain VR/AR Systems Integrated with Interactive Textile Devices, Electronic Interfaces, Power Supplies, and Display Hardware.
To fabricate different textiles Electronics with Advanced Electrical and Textiles Properties, Researchers have explored different methods. The Techniques can be generally categorized into two groups: Physical Methods and Chemical Methods.
The Train Includes Spinning, Printing, Coating, and Physical Vapor Deposition. The Printing Method has the Advantages of Low Temperature, Nonvacuum Operation, Low Production Cost, Potential for Large-Scale Manufacturing, and Wide compatibility with Materials.
Chemical Techniques Involve Chemical Reactions To Modify the Textile Surfaches Of Conductive Materials by Adding Chemicals or Controlling the Chemical Components of A Substrate. The Common Chemical Manufacturing Methods Included plating, Chemical Vapor Deposition (CVD), and carbonization.
One of the Key Components-and also a significant Challenge for Making Devices Truly Wearable-is the Energy Supply for All The Components of Vr and Ar Systems-Display Units, Controllers, Analog-to-Digital Converters, Wireless Modules, Sensing Units, and Computing Units.
Each of these components can work Separately or with Other Components through Wireless/Wired Communication Technologies. They also can be powered Separately Asy Need Different Levels of Power Consumption. Consequently, flexible batteries and supercapacitors are followed for Higher Power Consuming Devices Such as Displays, While Fabricsd Tribelectric Generators Are Promising Systems for Application in Self-Powered Sensing and Energy Harvesting.
For instance, last year researchers demonstrate an all-textile triboelectric sensor-based smart glove that was capable of capturing human gestures for remotry controlling a vr that enabled a teleoperated robotic gripper (journal of Materials Chemistry A, "An All-Text Sensor for Wearable Teleoperated Human-Machine Interaction ") .Arthough vr/AR Systems cannot be Complely Fabricated in textile structures (Yet), the authors believe that adopting certain devoted textiles Electronic Devices can provides Further User-Friendly immersive vr/ar experiences.
Concluding their review, they note that the Major Hindrances Today to the Progress of Textile Electronic VR/AR Systems are insufficient performance, Immature Production Technology, and Lack of System-Level Investigations and Standards. Also, the General Lifetime of Textile Electronics is Shorter That Of Rigid Microelectronic Devices and Many Textile Electronics Produced from organic or polymer Functional Materials are sensitive to water and oxygen, and the laundering processes of textiles can cause Deterioration of Function.
As is typical for this kind of early internship technology, Most Textile Electronics Experiment Have Been Conducted in the Laboratory or Research Stage, and Very Few Textile Electronics Have Been Commercialized So Far Because Many Devices Were Made Laboratory-Type Manual Techniques Instread of Factory-Type Machinery.
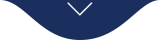