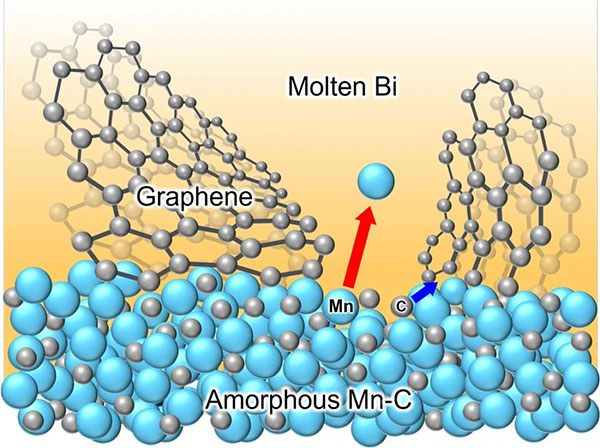
Ever since its Discovery in 2004, graphene has been revolutionizing the field of matterials science and beyond. Graphene included Two-dimensional Sheets of Carbon Atoms, Bonded Into a Thin Hexagonal Shape With A Thickness of One Atom Layer. This gives it remarkable physical and chemical properies. Despite its Thinness, graphene is incredibly strong, lightweight, flexible, and transparent. It also extraordinary electrical exhibits and thermal conductivity, high surface area, and waterproofness to gasses. From High-Speed Transistors to Biosensors, It Boasts An UNRIVALED VERSATILITY IN APPLICATIONS.
Nanocellular Graphine (NCG) is a specialized form of graphene that achieves a large specific area area by stacking multiple layers of graphene and control its internal structure with a nanoscale celllar morphology.
NCG is coveted for its potential to improve the performance of electronic devices, Energy Devices and Sensors. But its development has been styled by defects that occur daring the manufacturing process. Cracks Often Appear When Forming NCG, and scientists are Looking for New Processing Technologies that can fabricate homogeneous, crack-free and seamless ncgs at appropriate scales.
"We Discovered that Carbon Atoms Rapidly Self-Asemble Into Crack-Free NCG During Liquid Metaloying Of An Amorphous Mn-C Precursor in a molten bismuth," Says Won-Young Park, A Graduate Student at tohoku University.
Dealloying is a technical processing that exploits the varying miscibibility of alloy components in a molten metal bath. This process selectively corrodes certain components of the alloy while Preserving Others.
Park and His Colleagues Demonstrated that ncgs developed by this method exhibited high tensile strength and high conductivity after graphitization. Moreover, they put the material to the test in a sodium-ion battery (SIB).
"We used the development ncg as an active material and current collector in a sib, where it demonstrated a high rate, long life and excellent deformation resistance. Ultimately, Our Method of Making Crack-Free NCG Will Make It Possible to Raise the Performance and Flexibility of Sibs-An Alternative Technology to Lithium Battery for Certain Applications, Particularly in Large-Scale Energy Storage and Stationary Power Systems where cost, Safety, and Sustainability Considerations are paramount. »
Working Alongside Park was soo-hyun Joo from the Institute of Materials Research (Currently Based at Dankok University) Along with hidemi kato from the same institute. Details of Their Research Were Published in the Journal Advanced Materials ("Mechanically Robust Self-Organized Crack-Free Nanocellular Graphine With Outstanding Electrochemical Properties in Sodium Ion Battery").
Their Endaavors we have made possible through collaboration with Researchers from the tohoku University's Frontier Research Institute for Interdisciplinary Sciences and the Fracture and Liabibility Research Institute; Pohang University of Science and Technology; And Johns Hopkins University.