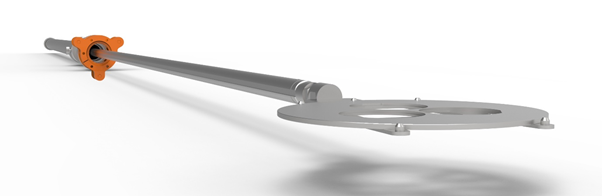
Certain areas of scientific research require atomically clean surfaces and low rates of contamination. In these instances, the ultra-high vacuum (UHV) environments are essential.
There are a number of unique challenges that UHV systems present to users, but possibly the chief concern for users is how they should best manipulate samples situated inside the evacuated enclosure. For the majority of applications, the most economical and reliable method of achieving this involves using a magnetically coupled sample transfer arm.
This article discusses key points to consider when choosing a magnetically coupled transfer arm intended for use in UHV applications.
Typically, the term ultra-high vacuum (UHV) refers to environments that have a pressure between 10-5 and 10-10 Pa. UHV is distinct from a high vacuum (HV), which ranges from pressures starting at around 10-1, extending to 10-5 Pa.5
For researchers using UHV systems, this pressure difference is obvious. In an HV environment, a surface will be entirely coated by a layer of contaminant gas or vapor in approximately 1 second. In contrast, surfaces in UHV environments will take approximately 1 day to be covered in this contaminant monolayer.1
This shows that UHV is essential for surface science applications because it is only possible to prepare atomically clean surfaces and study them at UHV pressures or lower.6 Multiple fabrication techniques also require UHV pressures to prevent contamination, such as atomic layer deposition (ALD), molecular beam epitaxy (MBE) and chemical vapor deposition (CVD).2,4
There are many surface analytical techniques that rely on UHV environments to allow the (relatively) free passage of photons, electrons, and ions that need to be measured. Such techniques include X-ray photoelectron spectroscopy (XPS), auger electron spectroscopy (AES), and secondary ion mass spectrometry (SIMS).
In a similar way, particle accelerators generally maintain UHV environments in order to allow particles to travel around relatively unimpeded. The vacuum system in place at the Large Hadron Collider, which maintains beamline pressures between 10-8 and 10-9 Pa, is the largest UHV system in the world.7
Challenges in Manipulating UHV Samples
UHV systems are carefully engineered to stop the outside from getting in, which presents significant engineering challenges where the manipulation or transfer of samples within UHV systems is concerned.
There are three commonly used methods to produce mechanical movement inside a UHV chamber:
A vacuum-sealed mechanical coupling through the vacuum wall
A magnetic coupling that transfers motion from outside the chamber to inside it
Or a sliding seal using specialized greases with low vapor pressures.8
Magnetically coupled transfer arms provide the most economical and reliable option for the majority of applications.9 These devices are very suitable for the manipulation of flag-style sample holders, as they allow for linear translation and rotation without needing sealed holes in the surface of the UHV chamber.
Manipulating Samples with Magnetically Coupled Transfer Arms
When planning sample transfer using magnetically coupled transfer arms, the type of motion that is needed is typically the first element that should be considered. Generally, mag-coupled transfer arms will only enable linear movement, or they will enable a combination of rotational and linear movement. Multi-axis transfer arms, such as the Elevating PowerProbe series from UHV Design, offer additional lift and lowering motions for sample collection and hand-off, meaning users can sometimes avoid the use of secondary motion tools.
In addition to these movement options, mag-coupled transfer arms provide users with several mechanisms that grip sample flags. For example, the PowerProbe range of mag-coupled transfer arms developed by UHV Design provides flag gripper mechanisms that are controlled by rotating the shaft, as well as flag toggle mechanisms that lock to the sample flag when it is rotated. Locking gripper mechanisms are also available, which are controlled by a separate rotating locking ring on the shaft.10
Once these decisions are made, it is essential to consider the mechanical performance of the transfer arm. By and large, transfer arms are subject to droop, deflection, and radial deviation simply because of their weight and stiffness. All of these issues can induce difficulties in sample handling if they are not properly addressed.
Droop is the term for the natural sagging of the transfer arm over full extension. When mounted to the chamber or load-lock, all sample arms are susceptible to bending under their own weight when they are fully extended.
Droop can be corrected using a port aligner, which enables the distance and angular relationship between flanges to be adjusted and aligned.Deflection is another associated phenomenon, which sees the transfer arm spring up when samples are unloaded, for example. To avoid vertical deflection like this, properly characterizing the deflection of a sample arm is crucial.Consider the following calculations:
With a 0.7 Kg substrate, the fork height will change by about 13 mm.
With a 0.7 Kg substrate and support at 600 mm, the fork height will change by less than 2 mm.
With a 0.4 Kg substrate, the fork height will change by about 7 mm.
With a 0.4 Kg substrate and support at 600 mm, the fork height will change by less than 1 mm.
Another type of deviation is known as radial deviation, which is also called arm roll. This is the uncontrolled, rotational movement of the sample arm as it undergoes linear motion. For the majority of applications, it is important to use a transfer arm that offers low radial deviation.HV Design is a specialist in the design, manufacture, and supply of market-leading HV and UHV motion and heating products. Their PowerProbe series of sample transfer arms was created to provide exceptionally smooth and accurate linear and rotary motion in UHV environments.
The PowerProbe series provides unparalleled coupling strength, exceptional axial stiffness, and zero-backlash under low loads. PowerProbe sample transfer arms are bakeable to 250 °C without the need to remove the outer magnetic assembly, and together offer researchers a huge range of movement and flag sample transfer options, which can be configured to work with any UHV application.
Découvrir